德州推荐分条整经机品牌
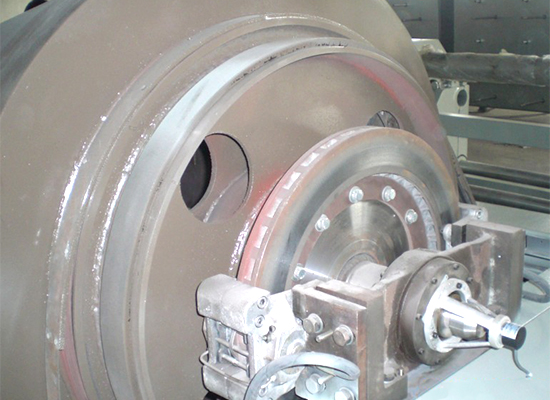
筒子架是重要部分,随着整经卷绕速度的不断提高,对筒子架的要求也越来越高。筒子架不仅要满足整经基本的工艺要求,而且还要尽量减少整经过程中纱线张力的变化,提高整经质量;尽量缩短换筒停机时间,提高整经机的生产效率。要满足高速整经和高品质纱线整经的要求,需要解决以下问题:一是纱线高速适应性,即较少经纱的断头率;二是要解决整经张力的差异性,提高纱线张力的均匀性;三是提高整经效率,减少围绕在筒子架上的辅助时间。目前,国内个别企业已经研制了大“V”型筒子架,数百个筒子退绕时的引纱路线在没有张力盘、没有导纱瓷眼和没有折角引纱的情况下,将摩擦减少到较低程度,有利于高速引纱。但如何减少经纱片的纱线张力差异,其中有一点很重要,就是要求所有的夹纱板制停同步性能好,大“V”型筒子架链条及其传动机构具有较高的传动精度,确保换筒定位准确;其次断纱自停监测器、吹风清洁装置的灵敏度和高效性,也是影响整经张力均匀性的重要因素。
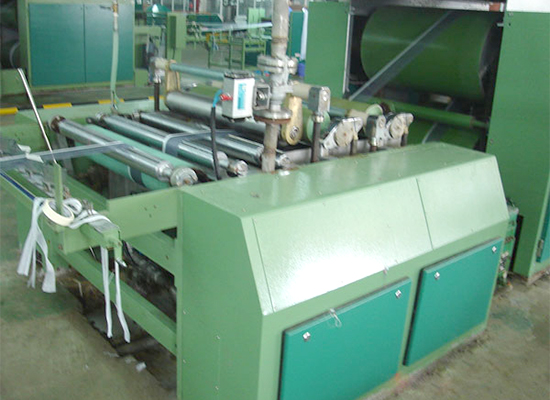
带有断纱时的夹纱装置、满轴(绞)电动剪纱装置等.整经筒子架已由单一的放置筒子功能逐步发展为新型筒子架所具有的纱线张力控制、断纱自停信号指示、换筒自动打结等多项功能。筒子架结构的不断完善,使整经速度、整经质量、生产效率得到提高。回转筒子的切向退绕筒子架。用于部分有边筒子的筒子架,由于筒子的惯性作用,使得张力变化大,故这种方式不宜于高速整经,整经质量差,筒子容量也受限制,很少使用。固定筒子的轴向退绕筒子架。固定筒子的轴向退绕简子架,使织轴纱线退绕条件大大改善,有利于整经速度及整经质量的提高,并使得筒子卷装容量增加,因此被广泛使用。
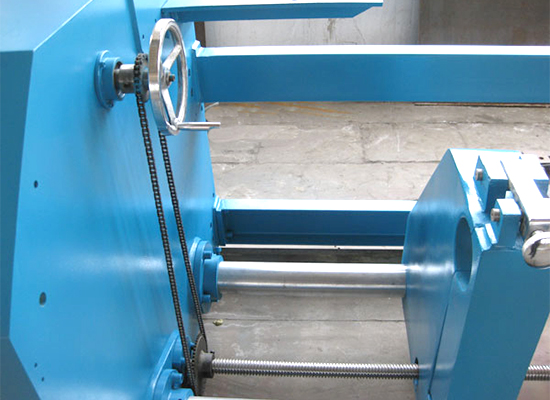
1、平行恒力加压卷绕,不跳轴,不浪纱,卷绕密度均匀;2、机械计长;3、主传动有额定速度和无级调速(供选);4、断经监控停车装置。采用全封闭集装落针式,设置在筒子架上,反应灵敏,断头不易卷入轴内;5、采用双柱刻盘式张力器,保证经纱张力均匀;6、主电机刹车采用新型电磁制动器(高新技术)制动灵敏;7、工作幅度:1400 1600 1800;8、控制车速:350m/min;9、筒子数量:640(可定制);10、锭矩:220×220(可定制)。
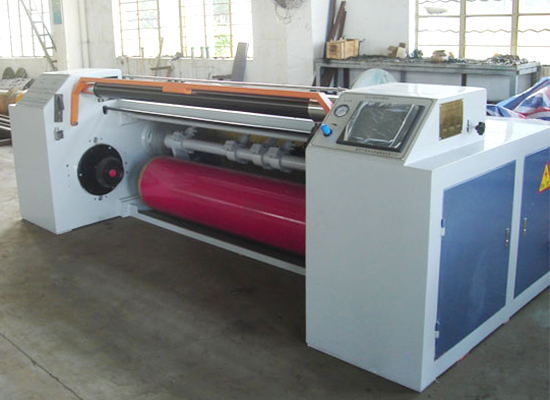
分段整经是将经纱平等地分别卷绕在狭幅的小经轴上,然后再将若干只狭幅小经轴并列地穿在芯轴上组装成织轴。然后安装到经编机上,供编织用。特点:生产效率高,占地面积较小,运输和操作方便,比较经济,能适应多品种、多色纱线的要求,随着分段整经技术的发展,分段整经向高速、智能张力控制、高精度拷贝方向发展,目前较高线速度可达1200米/分。将一经轴上所需的纱线根数分成许多份,再将经纱按所需的长度,一份一份地卷绕到大滚筒上,以后再由大滚筒卷绕于织轴上。(如2000根分10份,每份200根,一份一份分别绕到大滚筒上,然后再倒绕到经轴上)。特点:一次所需纱筒数少,占地面积小,效率低,操作麻烦。轴经整经是将经编机一把梳栉所用的纱线同时卷绕到一个经轴上,直接上经编机,供编织用。一般用于多梳栉经编机的纱线根数较少的花梳上。所以轴经整经有时又称“花经轴整经”。用途:适用于经纱叫根数不多的花色纱线的整经,不适宜于幅宽大的地组织经纱整经。轴经整经从较初的凸轮控制横移,发展到通过伺服电机来控制横移,并且能智能收边。
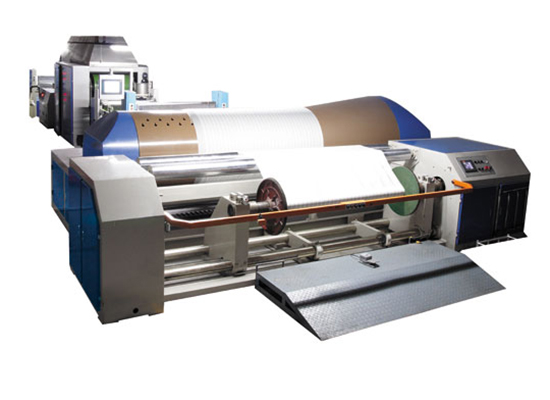
张力控制是整经设备控制系统中很重要的一个环节,主要是运用电子齿轮对经纱卷绕过程中的张力进行控制,保持整经张力的恒定。无论在生产效率方面还是在自动化操作方面,都在不断地改进和提高。恒张力控制技术主要包括磁粉恒张力控制、变频调速恒张力控制和伺服闭环恒张力控制。恒张力控制系统主要是以PLC或者单片机为控制核心,将速度和张力传感器采集来的信号进行处理,通过与最初设定的纱线张力值进行对比,按照PID控制策略对数据进行处理与计算,实时地调整反馈控制信号,通过调整交流伺服电机或者变频电机的转速保持整经张力的恒定控制。本文对比分析了上述三种恒张力控制技术特点,并对应用较为广泛、控制精度较高的伺服闭环张力控制系统进行介绍,探讨整经机恒张力控制技术的发展趋势。
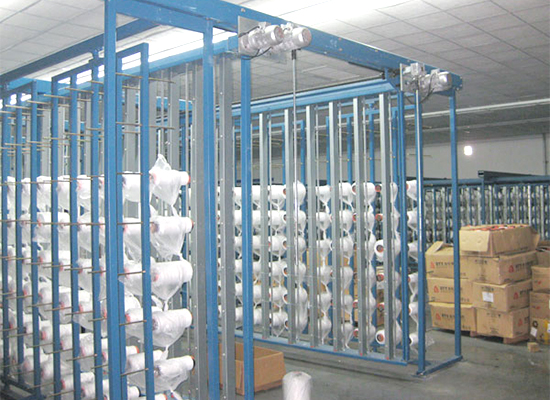
德州分条整经机在进行整经的过程中,工艺始终要求整经机的经轴传动能达到恒线速以及恒张力。这对于普通的整经机而言,要达到这个效果是非常困难的,而分条整经机的出现正好解决了这一难题,这主要是由于分条整经机采用了经轴直接传动的形式,从而能够获得高速和高质量的经轴。但是采用这种经轴直接传动形式也有优缺点。优点:分条整经机利用液压无级变速的形式使得油电动机传动经轴。此过程中,传动速比一般的范围要大。并且油电动机的转矩也是比一般整经机的大,所以容易启动,使得分条整经机能够实现恒线速以及恒张力的目的,并且在整个过程中,分条整经机可以做平稳而频繁的换向运动。推荐分条整经机缺点:这种经轴直接传动形式对液压系统元件的密封性有很高的要求,如果密封性不强很容易发生漏油的情况,所以操作人员在调机前都需要检查液压系统元件的密封性是否完好,不然等到分条整经机出问题的时候,排除故障要比机械传动还要困难。